Contents
Modular construction has gained significant traction in recent years as a cost-effective and efficient alternative to traditional building methods, especially for large scale projects. However, understanding how modular projects are priced and how to keep your budget on track can be challenging. With various factors influencing costs along the way, it's essential to be well-informed to make the most of your investment.
Cost Breakdown of a Modular Project
First, you need to understand the cost breakdown of a modular project as it’s quite different from traditional construction.
The following make up the largest components of your final cost:
- Site Preparation: Involves laying the foundation, installing necessary utilities such as water, sewage, and electricity, and building the first few floors.
- Factory Manufacturing: Anything that goes into the construction of the units in the factory. This includes wood or steel framing, drywall, appliances, and windows.
- Transportation: The cost to move the modules to the site.
- Module Installation: Involves craning the modules and securing them into place.
- Finishes (Interior and Exterior): Adding the final touches and implementing the agreed upon design
Depending on the decisions you make throughout the process, these costs can vary.
Factors that Can Influence Cost
There’s no cookie cutter formula for pricing a project nor can we give cost per square foot a numbers, but we can identify the most common factors that influence the final cost. This will help you make informed decisions when vetting properties or going through the design process of a modular project.
Factor #1: Distance from a modular factory
A large portion of a modular project is going to be allocated to transportation. The farther the construction site is from the modular factory, the higher the transportation costs will be. This includes not only the cost of fuel and driver labor but also any special permits required for transporting oversized loads.
Many modular companies run into the challenge of finding locations for their factories close enough to major cities, but far enough to where they can escape the high labor costs of those major cities.
But, companies like Volumetric Building Companies (VBC) have struck the perfect balance with each of their factories, serving cities like San Francisco, Philadelphia, New York, and even overseas in major cities in Europe, the Middle East, and even Africa.
Factor #2: Shape of property
The shape of the property can significantly influence the cost of a large-scale modular project.
An irregularly shaped property may require more extensive site preparation, such as additional grading, excavation, or retaining walls to create a suitable foundation for the modular units. These additional tasks can increase both the time and cost required to prepare the site.
Additionally, installing modular units on a property with an unconventional shape can be more complicated. Craning and positioning the modules might require specialized equipment or techniques, leading to increased labor costs.
Factor #3: Complexity of design
This is not to say that your project needs to be an exact replica of another. However, the level of complexity of your design can significantly influence the overall cost of a modular project.
“Not everything needs to be repeatable and so we're not trying to completely limit the magic of design flexibility at all, but we want to encourage repeatability where there's really high value in repeatability,” says Sara Pacelko, VBC’s Director of Product Design.
What Pacelko means is that incorporating repeatable elements into your modular project can help streamline the construction process and reduce costs without sacrificing creativity.
Remember, in a factory, processes and machinery need to be reset for every new design which can elongate the construction process. By standardizing certain components and systems, you can achieve efficiencies in manufacturing and installation that keep your budget in check.
For example, if you are building a hotel, limit the variety of room layouts. Instead of offering over 20 different room types, you can cut down the number to around three or four distinct layouts. Your project will surely still be show-stopping, like this famous vacation lodge in Germany.
How to Keep Your Budget on Track
No developer likes a surprise cost that will blow a budget. Thankfully, the factory setting of modular construction offers more predictability and flexibility during the most crucial parts of the process. Regardless, it's essential to take proactive steps to ensure your budget stays on track throughout the project. Here are some key strategies to help you manage costs effectively:
Choose a factory close to the site
As we mentioned before, transportation will make up a large percentage of your final project cost. By finding a modular company with a factory located close to your site, you’ll unlock significant savings by cutting down the distance.
Have a contingency budget
The factory setting of a modular project eliminates any risk or delays caused by weather, a common obstacle that traditional construction faces. However, it’s still a good idea to incorporate a contingency budget to account for any unforeseen expenses.
Unanticipated costs can arise from a variety of sources, such as unexpected site conditions, changes in design or materials, and regulatory adjustments. By setting aside a contingency fund, typically around 10% of the total project budget, you can ensure that you are prepared to handle any surprises without jeopardizing the overall project timeline or financial stability.
Stay on Track with VBC
VBC has been a leading modular manufacturer for over ten years building affordable housing, hotels, student housing, and more all over the globe. Our team consists of designers, engineers, and other modular professionals equipped with the experience to streamline your construction process very step of the way. You can trust VBC’s expertise to keep your project on budget and on schedule.
Contact us today to learn how we can partner with you on your next modular construction venture.
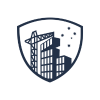