Contents
It’s the age old question we get in the modular construction industry: is modular construction actually cheaper?
The short answer? It depends. There is a time and place for modular construction. While it can offer significant cost savings in the right circumstances, factors like location and site conditions can play a role. But, when those factors align, you’ll discover that modular construction offers a lot more than affordability.
Let’s break down when modular truly shines—and when it might not be the best option for your budget.
What is Modular Construction?
Modular construction is often recognized in the single-family housing sector, but it’s quickly becoming the preferred method for large-scale construction projects like 100+ unit apartment buildings, hotels, student housing, and even medical facilities.
The term “modular” refers to the individual rectangular modules that are constructed off-site in a factory. Meanwhile, a separate team prepares the foundation and the first several floors of the project. Once the site is ready, the modules are ready to be transported and craned into place.
But, don’t let the term “rectangular” fool you. Technology and engineering have come a long way since modular construction got its start. Today’s modular designs are highly customizable, allowing for complex architectural features, various floor plans, and innovative materials. Modular buildings can now seamlessly integrate unique shapes, facades, and even environmentally-friendly features like solar panels and green roofs—proving that “prefabricated” doesn’t mean limited or simplistic.
With an understanding of how modular construction operates, when and where do the cost savings come in?
Key Factors That Make Modular Construction Cheaper
The defining factor of modular construction is the integration of a factory, and that just so happens to be the magic key to the cost savings and flexibility of this construction method. Let’s dissect.
Labor
When a modular company such as Volumetric Building Companies (VBC) is shopping for a new factory location, there is a lot of analysis and consideration that goes into it. At the top of the list, the factory must be in a location with lower labor rates.
By choosing areas with lower labor rates, companies can control production costs, which directly impacts the overall affordability of modular construction. This strategy allows modular companies to pass the savings on to customers, making high-quality, cost-effective building solutions more accessible to developers and homeowners alike.
Faster Construction Timeline
One of the biggest advantages of modular construction is its speed. Weather, site issues, or supply chain disruptions often delay traditional construction projects. Modular construction, on the other hand, takes place in a controlled factory environment where work can continue regardless of external factors.
While the modules are being built off-site, site preparation, and foundation work can happen simultaneously, drastically reducing the overall construction timeline. This parallel process allows projects to be completed up to 50% faster than traditional builds, which translates into significant labor and financing costs savings. Faster completion means getting your building operational and generating revenue sooner, making modular construction not only a time-saver but a cost-saver as well.
Economies of Scale
Modular construction benefits greatly from economies of scale. In a factory setting, materials for multiple projects can be purchased in bulk, which reduces costs compared to ordering for individual builds as needed, like in traditional construction. This ability to buy large quantities at lower prices means modular companies can optimize material usage and minimize waste, keeping production costs down.
The factory setting also allows for the storage of surplus materials. Traditional construction often faces delays and higher costs because materials are ordered only when needed, leaving projects vulnerable to price fluctuations or shortages. Modular factories, however, can stock up on materials in advance, ensuring that production continues smoothly and at a lower cost. This efficiency is a key factor in why modular construction can often deliver projects more affordably than conventional methods.
Standardization of Process
The standardization inherent in modular construction is a major contributor to its affordability. In a factory environment, the process of building modules follows highly regulated, repeatable steps, ensuring consistency and precision across all projects. This streamlined approach eliminates many of the inefficiencies found in traditional construction, where each project may require custom designs and varying workflows.
Furthermore, the controlled factory setting ensures fewer errors, meaning fewer costly reworks and delays. This level of efficiency and predictability is what allows modular construction to deliver high-quality results at a fraction of the cost and time of traditional building methods.
So, all of this sounds fantastic, but as we mentioned before, modular construction won’t be the right option for every project.
When Does Modular Construction Not Make Financial Sense?
While modular construction offers many cost-saving advantages, it's not always the most financially viable option for every project. Several factors can tip the scales, making traditional construction a more suitable choice in certain situations.
Site is Too Far From a Modular Factory
The modules have to make their way to the site somehow. Modules are often transported to the site by road on flatbed trucks. The farther the modules have to travel, the higher the cost.
Transportation expenses can add up quickly, especially if the site is located in a remote area or far from the nearest modular factory. Additionally, long-distance transportation may require special permits, escorts, and larger vehicles, further increasing costs. In some cases, these logistical challenges can negate the cost savings of modular construction, making it less financially viable for projects that are far from manufacturing hubs.
That’s why VBC is so selective of it’s factory locations. For example, wanting to serve the Bay Area of California where there is an extreme housing shortage, VBC has established it’s factory just an hour away in Tracy, CA. Check out more of VBC’s factory locations here. VBC has factories near multiple construction hot spots globally, offering modular construction where it’s needed most.
Site is Already in a Low-Cost Area
One of the key advantages of modular construction is its ability to reduce labor costs by building in factories located in regions with lower wages. However, if your construction site is already in a low-cost area, the financial benefits of modular may not be as significant. In such cases, traditional construction might offer similar savings on labor without the added costs of transporting modules to the site. When local labor is affordable and easily accessible, the price gap between modular and conventional methods narrows, making traditional construction a more attractive option for certain projects.
Best Project for Modular Construction
To summarize, modular construction is best suited for projects in high-labor cost areas with a modular factory located nearby. It’s ideal for developers looking to speed up timelines, reduce waste, and save on labor and material costs. However, every project is unique, and it’s important to weigh all factors—such as location, design complexity, and transportation logistics—when deciding if modular is the right fit.
If you're wondering whether modular construction is the best option for your project, schedule a call with our team for a personalized assessment. We'll help you determine the most cost-effective and efficient approach to meet your building goals. VBC operates factories across the globe, strategically positioned to serve developers in numerous cities worldwide.
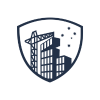