Contents
Let’s talk facts.
Traditional construction is too slow to keep up with the demands for affordable housing all over the world. Major cities are desperate for a new method that combines cost and time efficiency while also developing quality homes that will last for generations. Luckily, that construction method is already chugging along in full force.
Modular construction is quickly becoming one of the most preferred construction methods for large-scale developers in major cities from Los Angeles and the Bay Area of California, to the Middle East, Africa, and Europe.
But, as construction and design go hand-in-hand, there comes a new challenge to adapt the architecture process to accommodate the nuances of modular assembly. We sat down with Volumetric Building Companies’ (VBC) Director of Product Design, Sara Pacelko, to get her firsthand advice to effective design in modular construction.
How is Designing for Modular Different from Designing for Traditional?
Before we talk about the design, we need to understand how modular construction works. Modular construction involves creating volumes, commonly known as modules, of the full structure in an off-site factory. Meanwhile, a separate team works at the site to prepare the foundation and the first several floors. Once the modules are completed, they are transported by truck to the site where they are craned in place and assembled.
This simultaneous workflow, with factory work occurring while the site is prepared, reduces construction timelines by 30-40% compared to traditional methods.
Because of the utilization of modules, the design process is quite different.
“The biggest difference is that we're thinking about the pieces that make up a building in different scales. In traditional you have maximum amounts of flexibility, because your only limitations are code books, local municipality requirements, and zoning.” - Pacelko
Essentially, you need to understand how these modules are going to connect with one another as they’re being assembled. You are dealing with larger comprehensive pieces, while in traditional construction, the pieces you’re handling are relatively minuscule (drywall, nails, floorboards, etc).
Let’s look at a smaller scale example. Think about the different thought processes between installing pre-made cabinetry as opposed to building cabinets from scratch. With pre-made cabinetry, you’re focused on ensuring each unit fits perfectly within the designated space, considering the overall layout and how each piece will seamlessly connect. In contrast, building cabinets from scratch involves crafting each individual component, from cutting the wood to nailing it together, giving you the flexibility to make adjustments as you go but requiring more time and precision in the process.
With an understanding of the difference between the design processes, Pacelko dives into the key considerations and what to avoid when you start your modular project.
Don’t Forget About Interfaces
In modular construction, interfaces refers to how the modules relate to one another and other parts of the building. How modules come together in the final building is typically called site-assembly. This is obviously an important aspect of modular construction.
Examples of interfaces include module to podium; module to corridor piping; module to module at mate walls; module to module at exterior walls; module to module at roof. Each of these interfaces has necessary site completed activities to make the building whole, like structural connections, weather barriers, and fire stops.
A very common interface between modules is a minimum two inch gap, centered on building grid lines. This may not seem like a big deal, but when you consider that this two inch gap needs to be factored in in between every single module, it adds up. This means that for a multi-module building, these small gaps can collectively impact the overall dimensions, structural alignment, and even the aesthetic finish of the project.
Properly accounting for interfaces ensures that the modules connect seamlessly, maintaining structural integrity and achieving the desired look and functionality. It's these details that highlight the precision required in modular construction and set it apart from traditional building methods.
Think about Constructibility AND Manufacturability
“In traditional, the goal is constructibility, making sure the building as it's designed is constructible. But, when designing for modular, you also have to think about manufacturability. In the industry we call that design for manufacturing and assembly or DfMA.” -Pacelko
When designing a unit where modules are being manufactured, there needs to be an understanding of your manufacturers’ requirements based off their manufacturing practices. Different manufacturers can have different requirements for design for manufacturing, which makes it a little bit more complex than designing for constructibility. For example, each manufacturer may have different limitations on the max size of modules.
Manufacturers might also have specific preferences for materials, joint types, or connection methods that affect the design. This means architects and engineers must collaborate closely with manufacturers to ensure that the design can be efficiently produced in a factory setting and then assembled on-site. Integrating manufacturability and constructability into the design process helps streamline production, reduce waste, and create a more efficient and cost-effective building process.
Repeatability of Design
“I believe in flexibility where it creates high value for the customer, and repeatability where it provides the most time and cost savings. There is still design freedom and customer choice”
How does VBC accomplish this? The team has defined set unit layouts where the most complex part of the dwelling is completely modeled and coordinated with some customer choices for countertop heights, finish selections, and fixture types. This usually accounts for the first 24’-30’ of a unit from the corridor. The last 6’ of a unit is completely open for client and designer flexibility, allowing changes in façade treatments and building articulation. This translates to faster design time and reduced costs for clients.
This approach strikes a balance between efficiency and customization, ensuring that the project remains cost-effective without sacrificing the unique needs and preferences of the client.
If you’re worried about your project looking too similar to other buildings, rest assured that that won’t be a concern. The exterior of the building and the finishes are where the client can put their style and personality into the project, and really, that’s where the structure starts to build its character. Check out some of VBC’s projects and see for yourself. No two projects look alike!
VBC is the Leading Modular Manufacturer
Designing for modular construction requires a shift in perspective, focusing not only on the end result but also on the process of manufacturing and assembly. By embracing principles like DfMA, understanding the intricacies of module interfaces, and balancing repeatability with design flexibility, you can unlock the full potential of modular construction. This approach can lead to significant time and cost savings, higher-quality builds, and a more streamlined construction process.
Ready to transform your project? Contact VBC today to discover how our expertise in modular manufacturing and designing can bring your project to life. Our team of experienced professionals is ready to help you navigate the complexities of modular design and construction, ensuring your project is efficient, cost-effective, and built to the highest standards. Reach out to VBC to learn more about what we can do for your next project.
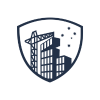