Contents
Global modular building specialist, Volumetric Building Companies (VBC), has announced ambitious plans to expand in the UK.
This follows VBC’s merger with Polish modular manufacturer Polcom earlier this year to extend its reach into Europe, and strategic acquisitions, which include the assets of the modular business Katerra, to facilitate efficient servicing of projects across the US.
VBC is on track to become a $1bn modular construction company over the next three years and is now targeting the UK build-to-rent, affordable housing, student accommodation, and hotel sectors.
Led by Vaughan Buckley and headquartered in Philadelphia, VBC is one of the world’s largest modular businesses. It offers advanced steel-framed modular and innovative timber construction technologies. Both solutions are highly efficient, cost-effective and have significantly less environmental impact than in-situ construction.
With proven capabilities in the multi-occupancy residential and hotel sectors worldwide, VBC uses a technology-enabled design and engineering model and precision manufacturing to deliver higher quality, highly sustainable offsite building solutions which reduce build programmes by up to 50 per cent. This approach is helping to address the chronic undersupply of housing globally.
Vaughan Buckley, CEO of VBC said, “VBC is set to become the leading provider of optimised, cost-effective, sustainable solutions for modular buildings around the world. We have tremendous capabilities in the engineering and delivery of advanced modular solutions and buildings which are fully finished and even furnished offsite. Having technology-led production facilities on multiple continents, we are now well placed to drive change, transform construction, and address the housing crisis in the UK, Europe, US, and globally.”
According to Andy Smith, UK Director of VBC, “Residential – both build-to-rent and affordable housing – is one of the fastest growing segments of the offsite sector, driven by the high cost of private rental, the lack of affordable housing, and changing demographics. There is a critical need to increase the housing stock in high density urban areas and to radically improve the productivity of UK construction.”
“We now have a dedicated management team in place in the UK and there are plans to secure offsite manufacturing capabilities here, in addition to our existing and extensive modular production resources in mainland Europe.”
“Our aim in the next three years is to secure a strong order pipeline in our target sectors in the UK – student accommodation, build-to-rent, affordable housing, defence, custodial, and hotels – and to raise the profile of VBC here, ahead of our expansion into Western Europe. We are already in advanced discussions with a number of hotel groups, private developers, major contractors, and social housing providers.”
“VBC has the resource and proven expertise in the industrialisation of construction, using a Design for Manufacturing and Assembly (DfMA) approach and data intelligence to drive continuous improvement. We have dominated the hospitality and affordable housing spaces in other countries with our innovative timber volumetric and steel-framed offsite solutions. We also manufacture ‘components’ inhouse – such as bathrooms and cabinets for kitchens and bedrooms – giving us complete control and security of supply for fixtures, fittings and finishes from design to manufacture, installation and handover.”
With strong financial backing and investment in place, VBC now has more than 500 employees and over 1.25m sqft of manufacturing space in the US and Europe. Its board has decades of experience gained from blue chip organisations including Google, BP, Harley Davidson, and PIMCO.
VBC also has more than 50 designers in its globally integrated multi-disciplinary design team and its highly innovative data-driven approach means its customers benefit from reductions in waste, faster design and build, and improved energy efficiency.
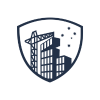