Contents
The construction landscape is evolving rapidly, and modular construction is emerging as a transformative approach. Yet, architects often approach modular projects with a mindset rooted in traditional construction. This disconnect can lead to inefficiencies, missed opportunities, and higher client costs. Here’s what we wish architects understood about modular construction and why it matters.
1. The Design Process is Fundamentally Different
When designing in traditional construction, most architects are familiar with a linear process. But because modular construction works on concurrent timelines, the design phase works a little differently.
Speed is the name of the game in modular construction, so the design process must be front-loaded to account for simultaneous workstreams. While the foundation and utilities are being built on-site, the modules are fabricated in a factory. This requires architects, engineers, and contractors to finalize detailed designs much earlier than in traditional construction, as any changes mid-fabrication can be costly and disruptive.
2. Modular Relies on Design for Manufacture and Assembly (DfMA)
In modular construction, the entire design process revolves around Design for Manufacture and Assembly (DfMA). This methodology ensures that each module is optimized for factory production and seamless on-site assembly.
Modules are prefabricated in a controlled factory setting, so they must be designed with precision to align perfectly when transported and assembled on-site. This means architects must account for constraints like transportation dimensions, structural reinforcement for lifting, and efficient integration of mechanical, electrical, and plumbing systems.
While these limitations might seem restrictive, DfMA also offers opportunities for innovation. Repetitive elements, like apartment units, can be designed for consistent quality and scalability, saving time and reducing waste.
3. Efficiency is Built into the Process
Modular construction thrives on efficiency, and architects who embrace this can achieve incredible results. Designing repetitive elements, such as hotel rooms or apartment units, allows for consistent quality and faster assembly.
One example of modular efficiency is the concept of mirroring, where designs for one module are mirrored to reduce manufacturing complexity. This can save significant time during production without sacrificing aesthetics or functionality.
Efficiency doesn’t mean cutting corners—it’s about finding smarter ways to achieve the same (or better) results.
4. Collaboration is Key
The success of a modular construction project depends on early and ongoing collaboration between all stakeholders. Unlike traditional construction, where trades can work sequentially and adjust plans on the fly, modular projects require architects, engineers, contractors, and manufacturers to work together from the very beginning.
Every component of a modular project—from structural design to plumbing and electrical systems—must be precisely coordinated to fit within the confines of the factory-built modules. Miscommunication or late-stage changes can result in costly delays, making collaboration essential.
The design team plays a pivotal role in bridging the gap between aesthetics and technical requirements, while manufacturers and contractors provide input to ensure the design is practical and buildable. Tools like Building Information Modeling (BIM) are often used to facilitate this process, enabling real-time collaboration and minimizing errors.
5. Modular is Not as Limited as People Think
Regardless of these differences, designing for modular construction isn’t as restrictive as most people think. New architects often assume modular buildings are limited to dull, blocky designs, but a quick glance at VBC’s modular portfolio quickly dispels that myth.
Modern modular construction techniques allow for diverse architectural styles, from sleek contemporary designs to charming traditional aesthetics.
With careful planning and the use of advanced tools like Building Information Modeling (BIM), architects can create dynamic, complex structures that rival—or even surpass—the design possibilities of traditional construction. Features like cantilevers and intricate facades can all be achieved with modular methods, proving that modular buildings are anything but cookie-cutter.
6. Budgeting and Cost Management Start Early
As mentioned earlier, in modular construction, the relationship between design and budget is more interconnected than in traditional construction. Because modular projects are built in factories with much of the construction happening off-site, the timeline for decisions is significantly compressed. This leaves little room for extensive changes or adjustments once the project is underway. For architects, this means that budgeting and cost management must be addressed from the outset, often even during the early stages of design.
Designing with a realistic budget in mind is not just about choosing the right materials—it also involves anticipating all aspects of production, from procurement to installation.
To ensure that the project stays on track financially, architects must keep the target cost in mind throughout the entire design phase. This involves finding a balance between the client's vision and the practical constraints of modular construction. Design elements should be selected based on their efficiency in the manufacturing process, and cost-effective materials should be prioritized wherever possible.
7. Integrated Furniture Manufacturing and Installation
Some modular manufacturers, like VBC, go a step further by offering integrated furniture manufacturing and installation alongside the modular units.
For architects, this integration provides significant benefits. First, it simplifies the design process by allowing for better coordination between the structure and the furniture. Instead of sourcing furniture separately, which can often lead to mismatches in scale or style, architects can work with the manufacturer to create pieces that are custom-fit for the modular units. This ensures a cohesive and functional interior from the outset.
Additionally, integrating furniture into the modular process allows architects to maximize space efficiency. Since the furniture is part of the design, it can be tailored to fit the modular layout, making the most of available square footage. This is especially valuable in smaller or more compact modular spaces, where every inch counts.
Ultimately, architects who embrace this integrated approach can create more efficient, well-coordinated designs that stand out
Why Architects Trust VBC
VBC is the leading global modular manufacturer, producing eye-catching large-scale buildings in some of the most bustling cities in the world. With a commitment to innovation, quality, and seamless integration, VBC empowers architects to create projects that are not only functional but also visually striking. By offering custom-designed, factory-built modules along with integrated furniture solutions, VBC helps architects streamline the design and construction process, saving time and reducing costs while maintaining the highest standards of design excellence.
Ready to learn more about how VBC can elevate your modular projects? Book a call with us today and discover how our collaborative approach can bring your design vision to life with unmatched efficiency and precision.
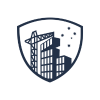