Contents
With high costs of labor and materials and salaries losing the race against inflation rates for the average American, it seems unlikely that affordable housing will become more accessible any time soon. At least not without technological improvements coming into fruition in the construction industry.
Luckily, a tried and true construction method has already made great strides in expanding possibilities in the housing industry. Modular construction has evolved since its inception to address the pressing need for affordable housing in a practical and efficient manner.
Modular construction has gone beyond building single-family homes and has crossed over to becoming one of the most favored construction methods for developers for everything from student housing to hotels and 500+ unit apartment buildings.
The Affordable Housing Challenge
It’s no secret that housing has become almost unattainable for the average American citizen. A combination of record-high inflation rates, the pandemic, job losses, and sky-high mortgage rates have many adults struggling to land on their feet.
According to Freddie Mac, home prices have continued to rise for the last 11 years. Home prices have increased by 18%, and even more in metropolitan areas like Los Angeles, which has seen a 30% increase in just the last five years.
Best case, adults opt to postpone moving out of their parent's house or move in with roommates in hopes of someday saving enough for a down payment. Worst case, they experience homelessness, which unfortunately has become a reality as we see the population of those without a stable home continue to rise. According to the National Alliance to End Homelessness, since 2017 the homeless population has risen each year by 6%.
Due to long construction times and high labor costs, developers struggle to keep pace with the ever-growing demand for affordable housing, resulting in an alarming gap between supply and demand. This problem has left many communities grappling with an acute shortage of accessible and reasonably priced homes.
A possible solution?
What is Modular Construction?
Also known as offsite construction, modular construction is a method in which the whole structure, or pieces of it, are built off-site in a factory. While the structure is being built off-site, a team of laborers prepares the site, demolition if needed, pouring the foundation, and prepping utility connections. Once the factory finishes building the units, they are shipped off on a truck to the site where they’re craned into place.
The final steps are swift as all that’s left is to finish connecting utilities and cleaning up the site.
Because many of the steps can take place at the same time, projects can be completed 30-50% faster than traditional construction methods.
Benefits of Modular Construction for Affordable Housing
While modular construction may not single-handedly solve the housing crisis outright, this construction method has the potential to ease some of the tension.
Reduced labor and material costs
Thanks to the controlled factory, modular construction significantly reduces costs when compared to traditional construction methods.
For starters, this factory method allows for efficient, assembly-line production of building components, minimizing the need for skilled labor on-site. This reduced reliance on highly specialized workers translates to substantial savings in labor expenses.
Adding to the savings, because of the standardized factory setting, modular factories benefit from bulk discounts for materials. This bulk purchasing power helps control costs and contributes to overall project affordability.
Because the structures are built indoors, modular construction also reduces the risk of delays and mishaps caused by disruptive weather.
Most, if not all modular companies will have a library of designs that you can choose from. While custom designs are still possible with modular construction, you’ll save a significant amount on design fees by choosing one of their standardized designs.
For example, VBC has a catalog of standardized studios, junior one-bedrooms, one bedrooms, two bedrooms and three bedrooms that can be stretched and optimized for things like gross rental income or construction cost.
This standardization of units saves time in the design process, allows for more accurate and transparent pricing up front, and creates consistency on the factory floor.
Shorter construction timelines
As mentioned before, modular construction is 30-40% faster than traditional construction.
This accelerated pace is made possible by the simultaneous processes. While the units are crafted in a controlled factory environment, site preparation, such as grading and foundation work, can proceed at the same time.
These shortened construction timelines bring significant advantages both to developers and those in need of housing. First, they lead to reduced financing costs, a critical factor for project feasibility, especially in affordable housing development. Second, faster project completion addresses the ever-growing demand for housing more promptly, easing the burden on individuals and families seeking affordable homes.
Better quality control
Modular construction excels in quality control, offering a level of assurance that's challenging to achieve in traditional construction. This advantage stems from the controlled factory environment where modular components are manufactured.
In this controlled setting, precision manufacturing ensures that every module is built with meticulous attention to detail, free from weather-related or on-site inconsistencies. Rigorous quality checks are conducted at each stage of production, from materials inspections to structural integrity assessments, ensuring adherence to industry standards and building codes.
Common Misconceptions of Modular Construction
In the realm of affordable housing, several misconceptions persist regarding modular construction. Addressing these misconceptions is crucial to understanding the true potential of this method.
Modular Construction is just for single-family homes
Modular construction has expanded far beyond modest-sized single-family homes.
In the realm of multi-unit developments, modular construction's innovative approach often involves stacking or assembling modules on-site to create large and functional complexes.
This method not only accelerates construction timelines but also enhances the overall efficiency of the project. It allows for the seamless integration of multiple units, ensuring that affordable housing solutions can be efficiently scaled to accommodate the growing demand for accessible and high-quality living spaces.
Modular Construction isn’t a sustainable business
Modular construction aligns perfectly with the demand for affordable housing by offering cost-effective, efficient, and quality-driven solutions. Its ability to expedite project timelines, reduce labor costs, and optimize material usage makes it not only viable but also highly sustainable in the affordable housing sector.
In fact, Volumetric Building Companies has been a titan of the industry for the last 10 years, and shows no sign of slowing down in the near future.
Modular construction isn’t built to last
Modular buildings are designed and constructed to meet or exceed the same stringent building codes and standards as traditional construction.
The controlled factory environment, precision manufacturing, and comprehensive quality control processes ensure that modular structures are robust, durable, and capable of withstanding the test of time. They are engineered to provide safe and reliable housing solutions for generations.
Modular construction isn’t flexible for what I need
Many people think that modular construction isn’t customizable, but this construction method is surprisingly versatile and adaptable.
While most modular companies will have standardized designs to choose from, most will allow customization for a wide range of design preferences. This will be more cost-effective, but if you’re looking for something truly unique or you have a difficult lot, modular manufacturers usually will have a design team that will meet with you to get the design that works best for you.
Modular Construction in Action
Skeptical?
VBC has a history of working with modular construction for a decade and has completed the largest modular project on the East Coast, 510 Broad Street.
If you live in Philadelphia, you’re probably no stranger to this eye-catching structure.
This project was done as a full service provide, including business development, design, manufacturing, installment, and finishes.
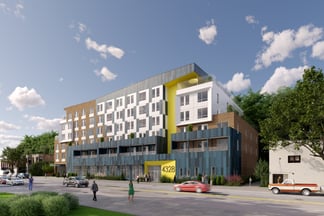
VBC’s impact reaches both coasts with a factory and full services offered in California. VBC’s first West Coast project can be found in Oakland. This five-story building over a podium was a huge success thanks to high-precision manufacturing and assembly in the nearby factory which utilizes European equipment combined with US construction knowledge.
The Future of Affordable Housing with Modular Construction
As skilled labor in construction declines and housing costs soar, modular construction emerges as the preferred method for affordable housing. This approach efficiently addresses the skilled labor shortage while streamlining construction timelines, reducing labor expenses, and offering budget predictability.
Learn more about affordable housing with Volumetric Building Companies (VBC)
VBC understands the immense need for affordable housing, which is why we’ve devoted years to research in refining this construction method.
We’re responsible for thousands of units delivered across the world and continue to put an emphasis on delivering a quality product. You can learn more about our process here.
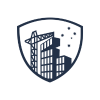