Contents
Special thank you to ICG for their contributions to this post.
When it comes to choosing the right modular manufacturing company for your project, doing your homework is essential. Not all manufacturers are created equal, and finding the right fit can make or break your timeline, budget, and overall quality.
Just like test-driving a car, you want to see how their factory operates and how your product will make its way through the process. Visiting the modular factory is a must. When meeting with your modular manufacturer while touring their facility, keep these five important questions in mind.
#1: What is the training protocol for employees?
The workers in a factory are the backbone of any assembly line. Their expertise and skill level directly impact the quality, precision, and efficiency of your modular project.
Ask about the factory’s training protocol to understand how workers are prepared for their roles.
- Are there ongoing training sessions to ensure up-to-date practices?
- Do workers receive specialized training in areas like quality control, safety standards, or equipment use?
A robust training program demonstrates a factory’s commitment to high-quality output and safety—key indicators of a reliable partner for your project.
If there is an absence of standard work protocols, the team will learn via tribal knowledge or learning from other members of the team. This works in the case of mentoring, but not long-term in a factory. Without standard work there can be no improvement because the base standard is absent.
This goes beyond the workers on the assembly line as well. Are supervisors and managers also following consistent, documented protocols?
#2: Do you see any workers sitting idly waiting for information or materials?
A minute or two here and there is fine, but excessive idle time on the factory floor can be a red flag, indicating inefficiencies in communication, workflow, or material supply. If workers regularly wait for instructions or materials, it signals potential delays, increased project costs, and a lack of organization. Observing whether teams are engaged in continuous work or frequently waiting can give you insight into the factory’s operational flow and readiness to handle your project efficiently. There is a very high value in consistency.
Additionally, if there is a bottle-neck, do workers know how to proceed or troubleshoot? Effective factories equip their teams with guidelines for addressing delays and bottlenecks, ensuring that workers can take corrective actions or redirect efforts productively.
#3: Is the team doing unburdened work?
In a factory, the work should always be coming to the worker and should be presented in a very ergonomic way.
If tasks require excessive reaching, lifting, or repetitive strain, it can lead to worker fatigue, slower production rates, and increased chances of error. Efficient factories design workstations that minimize physical strain, allowing workers to focus on precision and productivity without unnecessary burden. Observing whether tasks are ergonomically set up provides insight into the factory's commitment to worker well-being and process efficiency—both key to achieving consistent, high-quality results.
Here are some positive signs of an ergonomic work station:
- Tools and materials are within easy reach, reducing the need for workers to stretch or strain.
- Adjustable equipment allows each worker to customize their station to a comfortable height or angle.
- Clear, organized layout minimizes movement, so workers can perform tasks efficiently without unnecessary steps.
- Anti-fatigue mats or cushioned flooring to reduce strain on legs and feet.
- Proper lighting ensures workers can see clearly without eye strain or awkward positioning.
- Well-designed seating or standing supports that encourage good posture and reduce discomfort during longer tasks.
#4: Is there an hour-by-hour tracking system?
An hour-by-hour tracking system is essential for monitoring progress in real-time, identifying issues early, and ensuring that each step of production stays on schedule. With this system, the team can quickly address any slowdowns or disruptions, keeping projects on track and reducing costly delays.
Talk to at least one supervisor on the floor to gain insight into how this information is being tracked. Ask them how they use this data to manage workflow, address delays, and support continuous improvement. Are there regular check-ins to assess and adjust production pace, or protocols to resolve bottlenecks as they arise?
#5: Are safety protocols being met?
Worker welfare is paramount—not only for protecting individuals but also for maintaining consistent production. A single safety incident can halt operations indefinitely, leading to costly delays and project setbacks. Ensuring that proper safety measures are in place, from protective equipment to clear emergency protocols, minimizes these risks.
Some examples include:
-
Personal Protective Equipment (PPE)
-
-
Hard hats: To protect against head injuries from falling objects.
-
-
-
Safety goggles: To shield eyes from dust, debris, and hazardous materials.
-
-
-
Gloves: To protect hands from cuts, abrasions, and chemical exposure.
-
-
-
Ear protection: Such as earplugs or earmuffs to reduce noise exposure in loud environments.
-
-
Clear Signage: Informative signs indicating safety protocols, hazard warnings, and emergency exits placed throughout the facility.
-
Safety Barriers and Guardrails: Installed in areas where there is a risk of falls or accidents, especially near elevated platforms or open edges.
Most importantly, modular factories are full of advanced machinery that assist with efficiency and consistency, but a lot of this machinery requires heavy safety training or even a certification.
Depending on your country, there may be location specific safety regulations that must be met as well. Make sure to read up on these before visiting a factory so that you are aware of what to look out for.
Schedule a Modular Factory Visit
By asking the right questions and observing key indicators, you can ensure that your project is in capable hands.
If you're ready to see these principles in action, we invite you to visit one of Volumetric Building Companies’ (VBC) modular factories. With locations on both the East and West Coasts of the United States, as well as in regions across Europe, you can witness firsthand our commitment to quality, safety, and innovation. Schedule a tour today to explore our state-of-the-art facilities and discover how we can help bring your modular project to life.
Want the whole webinar where experts discuss the five questions to ask?
Click here to watch the webinar featuring VBC's own Helena Lidelow and ICG's Nick Masci and Melissa McEwen!
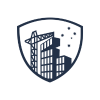