Contents
If there’s one thing that modular construction is known for, it's speed.
But, when you’re shaving up to 60% off of the usual timeline for a large scale project you’re bound to draw some skeptics. Is modular construction actually that fast?
After over a decade in the industry, you can trust us when we say that modular construction's speed is not just a myth. It’s a proven method backed by multiple successful projects and satisfied clients all over the globe. Where does that speed come from? We’re breaking it all down right here.
Understanding Modular Construction in Large Scale Projects
Modular construction is most familiar among single-family projects, but has taken over the large-scale development industry. This innovative building method involves constructing sections of a building, or modules, in a controlled factory environment. In the meantime, a group of builders prepare the site and the first several floors. The modules are then transported to the construction site and assembled into a complete structure.
With the modules in place, all that’s left is to complete the exterior design and connect the utilities.
Modular Construction vs Traditional Construction
So why is modular construction so much faster than traditional construction? The secret (although it’s not much of a secret) lies in the factory.
Traditional construction must be completed on-site on a linear timeline which means that each floor needs to be completed one after another. If it begins to rain or delivery of a necessary material is delayed the entire project gets stalled. All you can do is patiently twiddle your thumbs for weeks or even months until the issue can be resolved.
With the completion of your project getting pushed, you delay the opportunity to collect revenue. Additionally, you’ll likely have to extend the amount of time you pay fees for road closures and other city fees. It’s a tough situation overall.
Modular construction, on the other hand, rarely runs into these delays. Even without delays, modular construction still is leagues ahead in time efficiency.
The factory setting allows for simultaneous workflows. While a team works on the site preparing the foundation and building the first set of floors, another team in the factory builds the modules. This alone can cut out up to a year of your project timeline, but there are other benefits that make modular construction an attractive option.
Why is Modular Construction Faster?
Standardized assembly-line process
Modular manufacturers like Volumetric Building Companies (VBC) have fine-tuned their assembly-line process in their factories, ensuring that time and material is used as efficiently as possible. As a result, these factories can produce multiple modules a day.
No weather delays
As we mentioned before, traditional construction is often at the mercy of weather. Thanks to the factory setting of modular construction, a bit of rain won’t stall module production. Modular construction continues uninterrupted, ensuring consistent progress regardless of external conditions.
Bulk ordering of materials
Since most general contractors in traditional construction don’t have storage facilities, they can only order materials as needed for each project. This can be tricky as the cost of materials can fluctuate and availability can be inconsistent, leading to lengthy delays and increased costs.
Factories on the other hand? The perfect storage space. Modular factories are built with the capacity to store bulk items so that they can hit the ground running asap. No waiting for shipments.
All-in-one service
Companies like VBC really streamline the process by completing as much as possible in the factory. From painting and drywall to even building and installing furniture, they handle it all before the module ever hits the site. This all-in-one approach means fewer subcontractors and less on-site coordination. The result? A more efficient construction process that can save a significant amount of time compared to traditional methods.
Some people would scoff at the idea of mass-produced furniture, but VBC ensures quality materials and sturdy construction built for long-term use. Furniture can be designed to match the look and feel of your building ensuring cohesion in style. Not convinced? Check out this modular hotel in Germany that includes stunning furniture built to match the tropical feel of each room.
Now that you understand the efficiency of modular construction, let’s breakdown the timeline step-by-step.
Modular Construction Timeline
While each modular manufacturer has its own process, here’s how Volumetric Building Companies (VBC) manages the timeline for successful projects across major cities worldwide:
Step 1: Schematic Design
We kick off with a weekly Studio meeting. During this phase, our Studio team collaborates with the client’s AOR to gather critical inputs such as window legends, louvers, and roof loading requirements. We also provide an initial logistics plan, culminating in a schematic design sign-off.
Step 2: Design Development
In this phase, we refine the design and finalize decisions. Clients confirm their production slot while Building Information Models (BIM) are created and Quantity Takeoffs (QTO) are released.
Step 3: Construction Documentation
Here, we finalize the modular specifications. Our long-standing partnerships with structural engineers, life safety experts, and MEP consultants ensure that all construction documents meet the highest standards.
Step 4: Approvals Permitting Phase
Construction drawings are reviewed and approved by engineers, with final approvals from local authorities. With approvals in hand, we move into manufacturing.
Step 5: Mobilization
We prepare for manufacturing by conducting a full project review, purchasing all necessary materials and finishes, and completing the manufacturing shop drawing BIM model. The project is then set for production.
Step 6: Manufacturing
During manufacturing, the project goes through VBC’s assembly line. Each module is inspected, stamped by state authorities, and undergoes rigorous quality control before being wrapped and prepared for delivery.
Step 7: Transportation, Set & Construction
Modules are delivered to the site, staged, and set according to the project sequence. VBC handles transportation and setting globally, though clients can also opt to use their own services.
Ready to Start Your Modular Project?
With a streamlined process designed for efficiency and success, VBC is your go-to partner for transforming your modular construction vision into reality. From initial design through to final installation, our expert team is committed to delivering high-quality, timely results for your large-scale projects.
Don’t let the complexities of traditional construction slow you down. Contact us today to learn how our innovative modular solutions can speed up your project and bring your development to life.
Get in touch with VBC and let’s start building your future.
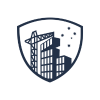