Contents
In the ever-changing landscape of construction and housing development, it’s inevitable that new technology and methods will arise to keep up with demand.
Modular construction is no exception. In fact, it’s the poster child for innovation and adaptability in the industry. This under-appreciated method has come a long way from its beginning, surpassing traditional construction in many facets like cost, affordability, and quality.
With more challenges arising in the supply chain and housing affordability on the rocks, modular construction is quickly becoming the favored method among developers, investors, and civilians.
From its humble beginnings to its current role as a sustainable and cost-effective building solution, let’s dive into the progress and developments we’ve seen over the decades.
What is modular construction?
Modular construction refers to the process of constructing a structure in a different location from the intended final location. A few modular companies, like Volumetric Building Companies (VBC), are able to construct up to 95% of the structure in their factory.
The structure (or structures) are then shipped to the site by truck.
Upon the arrival of the structures, a team of builders works to make the final utility installations and any finishing touches.
Benefits of Modular Construction
Over the last few decades, modular construction has been picking up speed for large-scale projects like hotels and affordable housing apartment complexes. Let’s break down what makes this method so lucrative:
- Faster construction - unlike traditional construction that follows a linear schedule, modular construction allows for multiple jobs to be done simultaneously, cutting down the project timeline considerably. For example, a team of workers can prep the site while the structure is built in the factory.
- More affordable - modular construction saves in both labor AND material costs. Since the modules are constructed through a standardized factory process, it’s much easier to train workers, rather than hiring costly skilled workers that are growing more scarce. Further, modular factories can take advantage of bulk discounts on materials due to their high production output.
- Higher quality control - quality assurance is difficult to implement in a traditional construction site, but in a module factory setting, processes are subject to regular quality checks and material inspections.
- Less weather disruptions - most contractors and developers will attest that weather delays are the bane of any construction project. With modular, the controlled indoor factory environment ensures that construction can continue regardless of forecasts. In states like Washington or Oregon that experience rain almost year-round, this is an advantage that can’t be beaten.
This list only scratches the surface of the benefits of modular construction…
The Humble Beginning of Modular Construction
One of the earliest documentation of modular construction was during the Gold Rush of 1849. Pioneers making the trek to the new region needed shelter that could be erected quickly and withstand for decades as their new home. To address these needs, prefabricated and modular construction techniques emerged as a practical solution. Families were making the trip with their modular components, including pre-cut and pre-assembled building materials. This allowed for quicker and more efficient construction of homes.
The following waves of modular construction shined after various wars, as nations experienced steel and labor shortages, creating a need for a quick and easy solution for building housing. Luckily, modular construction was the essential solution
Homes and other infrastructures could be built with reduced labor requirements and the utilization of more readily available building materials. The versatility and adaptability of modular construction played a pivotal role in helping nations rebuild and recover, solidifying its position as a reliable and transformative approach in the construction industry.
This method only continues to evolve in a positive way as new technology is introduced.
Predictions for Modular Construction
The future of modular construction appears promising, with several key factors influencing its growth and adoption in the coming years. Modular construction isn’t just for building single-family homes anymore. It’s now become a preferred method for erecting structures as large as 500+ unit apartment buildings, hotels, student housing, and more.
The solution for labor shortages
With a significant labor shortage currently impacting the construction industry, modular construction is in a position to gain popularity once again. The prediction is that "the market value for modular construction in new construction alone could reach $130 billion in Europe and the US by 2030."
This projection emphasizes the growing recognition of modular construction as an efficient and practical solution to counter labor shortages.
Meeting the demand for affordable housing
The increasing demand for affordable housing presents another catalyst for the rising popularity of modular construction.
Modular construction is on average 30-40% faster than traditional construction. Time is a critical piece to addressing the affordable housing shortage, so when a project can be done for a fraction of the time it would take for traditional construction, it’s a no-brainer.
New technologies in factory equipment are only shortening the timelines even further. VBC factories are equipped with new European equipment, increasing productivity and efficiency far beyond what was possible before.
Advancements in technology and methods
Speaking of technological advancements, new innovative methods now allow for more customization in modular construction.
Companies, like VBC, are transforming the modular buildings marketplace, now offering business development services and custom designs in addition to larger libraries of predesigned models.
Modular building methods have evolved significantly from their original utilitarian designs, dispelling the stereotype of blocky boring structures.
Now, modular constructions feature unique and attractive designs, reflecting the changing aesthetic preferences and design possibilities. Take this CitizenM London hotel for example.
Most would never have guessed that this unique building was constructed primarily in a factory, with each module being assembled on-site like a Lego set.
These trends are expected to catalyze a reimagining of modular construction's potential, extending its influence beyond its current boundaries, especially in regions where affordable housing is a dire need.
Markets Where We Predict Modular Construction to Skyrocket
Bay Area
In the tech-driven hub of the Bay Area, modular construction is poised to revolutionize the construction landscape. Rapid urban development and a booming tech industry have created an immense demand for efficient and innovative construction methods. Modular construction's potential to meet this demand while addressing housing shortages makes it a prime candidate for significant growth in the Bay Area.
Philadelphia
Philadelphia's rich history meets the modern era with modular construction. Known for its iconic architecture, the city is turning to modular methods to preserve its heritage while responding to the need for cost-effective and sustainable construction.
You may not have realized it, but modular construction has already started its takeover in this city. VBC has completed multiple large-scale projects in Philadelphia.
New York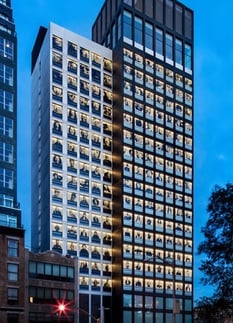
New York is no stranger to embracing new technologies, and modular construction is no exception. In fact, New York is already home to the highest modular hotel in the world, which clocks in at 52,958 sq ft and holds 315 livable units.
With limited space and sky-high property values, the city demands innovative construction solutions. Modular construction not only offers speed and efficiency but also aligns with New York's commitment to sustainability.
Los Angeles
Los Angeles, a city known for its creativity and innovation, is looking to modular construction to address its housing challenges.
According to US News, Los Angeles holds the largest homeless population and has shown a 2% increase between 2020 and 2022. Rapid population growth and the desire for affordable, sustainable housing make modular construction a natural fit. As the industry evolves, Los Angeles is set to see an upsurge in modular projects catering to its diverse communities.
London
Modular construction is making waves in this historic city, offering a combination of tradition and innovation. With housing shortages and sustainability in focus, London is becoming a hotspot for modular building, promising a future of elegant and efficient construction.
Munich
Munich, renowned for its engineering excellence and precision, is embracing modular construction with enthusiasm. As Germany's economic and technological hub, the city sees modular construction as a way to meet growing housing and commercial space demands. Expect to see Munich evolve with sleek and efficient modular buildings enhancing its urban fabric.
VBC Leads the Pack in Modular Building Methods
VBC has always recognized the potential of modular construction and has worked tirelessly to dispel the myths. Their work reflects the success of their numerous projects around the world.
VBC has been a leader in building large-scale affordable projects with modular building methods for a decade now and continues to make its mark in new regions where it's needed most.
If you’re interested in bringing the efficiency and possibilities of modular construction to your city, take our quiz to see if this progressive building method is the right solution for your project.
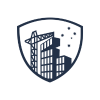